We built our last house with the goal of being net-zero energy.
The West Asheville lot is a small 0.08-acre infill lot with great southern exposure. That allowed for both solar photovoltaics and passive solar design on our three-bed, two-bath, 1,416-square-foot home.
The house was designed for passive solar to help with heating, with good roof configuration for solar panels (but low-enough height to avoid obstructing a neighboring home’s existing solar panels) and a bermed lower level with good natural light.gy star
Our building strategy was typical green building fare: high insulation values in the envelope, good air tightness coupled with ventilation, as well as efficient appliances, heating and air conditioning equipment.
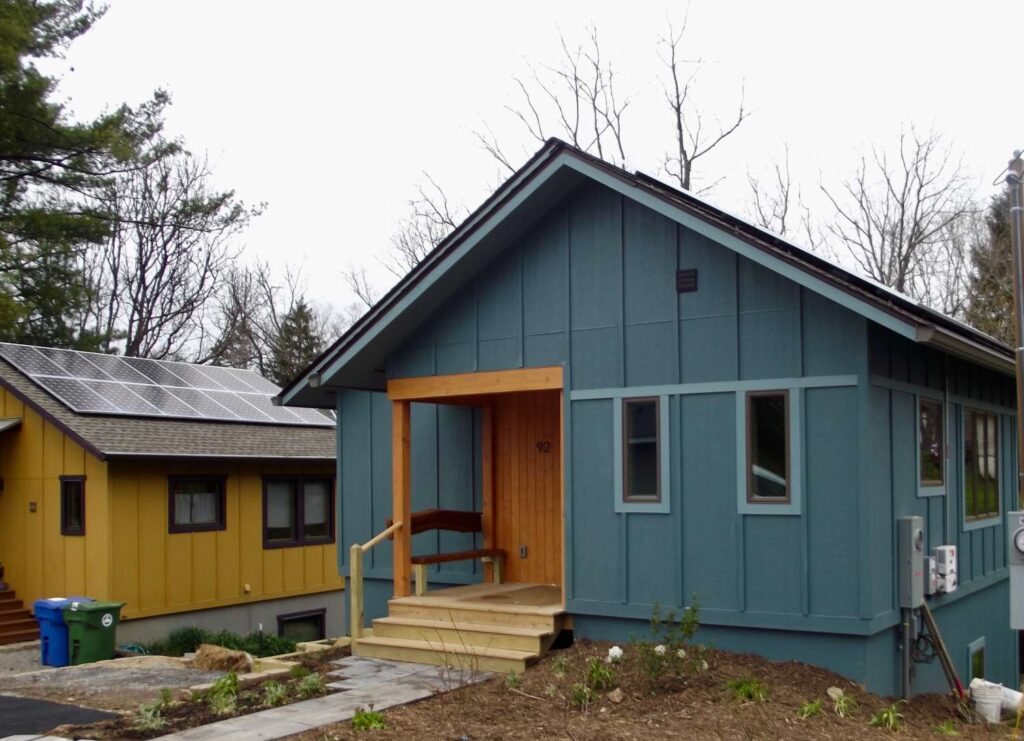
The lower level walls are precast concrete that come with R-12 foam insulation. R-19 fiberglass batts were installed into the wall cavities for a total of an R-31. The concrete floor has has R-10 underneath and R-5 around the perimeter. Additionally, we added closed-cell foam around the bottom perimeter to insulate and seal the bottom beam and behind the concrete floor edge where the bottom of the wall connects to the floor. Closed-cell foam was also blown in around the downstairs bathtub to seal and insulate. Lastly for the downstairs, open-cell foam was blown in around the rim joist to insulate that section between the floors.
Upstairs, we framed the walls with 2×6 studs on two-foot centers and sheathed it with Zip R Panels that have one inch of R-6 polyisocyanurate foam. These panels provide a thermal break, water and air barrier and help with any possible condensation on the exterior sheathing. In my mind, they work somewhat like a gasket that helps slow air infiltration.
Cellulose was blown in the stud bays resulting in R-29 for the upstairs walls. The windows were Andersen double-pane windows (U-Value: 0.270, SHGC: 0.210). Though triple-pane would have reduced the energy demands some, it didn’t seem like a cost-effective improvement.
We used raised-heel trusses for a flat ceiling. The raised heel was sheathed on the outside with the Zip R panels for a thermal break at the ceiling joists and top plates of the walls.
The insulation company also sealed in the attic space with closed-cell spray foam at the partition walls and penetrations in the sheetrock at the electrical boxes and fixtures. We blew in R-60 cellulose insulation. The attic is vented with ridge and soffit vents.
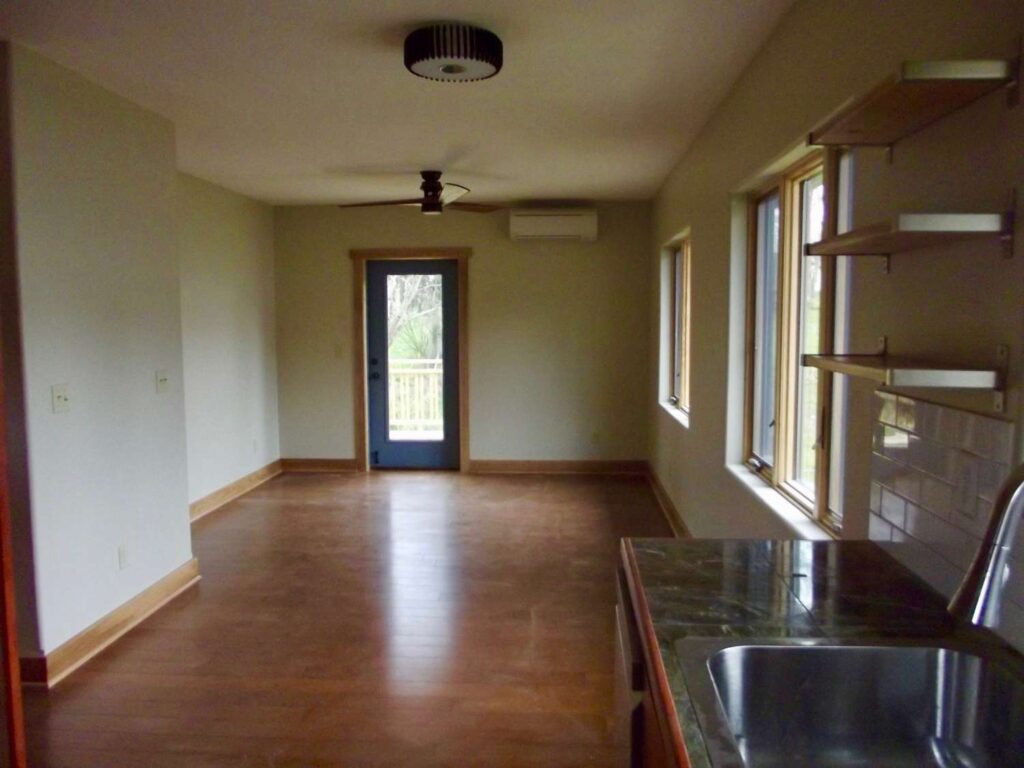
We also kept the energy demand down by installing a heat-pump water heater; ductless mini-split rated at 12.2 HSPF and 17.7 SEER; all LED lights; and ENERGY STAR®-certified appliances including an induction cook stove, dishwasher, and refrigerator.
The one thing we did not choose that would have helped the energy equation was a heat-pump clothes dryer. Not only are they more efficient at drying the clothes, they do not vent outside so they don’t cause conditioned air to be exhausted to the outside. A drawback is the cost of the unit, though some of the extra cost could be saved by not having to install a vent that is needed for a conventional dryer. They do take longer to dry clothes, which might be a factor for a large family.
With all the systems in place and the solar sized according to earlier modeling, we contracted for a 5.68-kW array that we expected to produce as much as or a little more than the annual consumption.
In fact, according to the final HERS model, the house is -8 (HERS 45 before PV). This suggests a small surplus of solar generation, though that will be dependent on how the occupants operate the home.
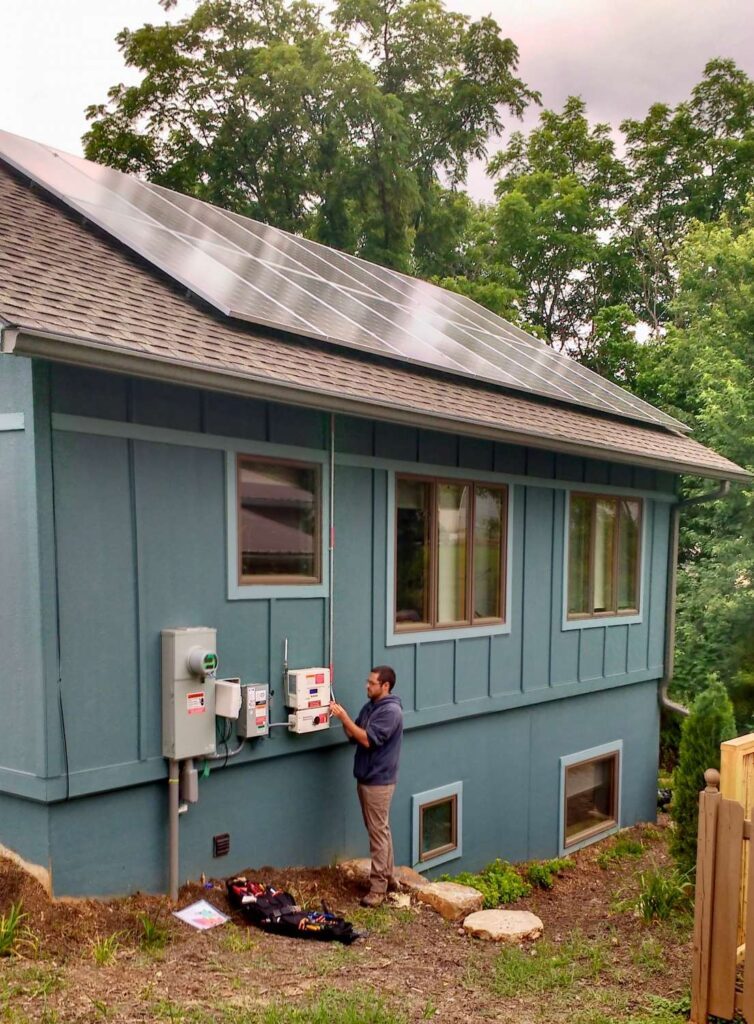
The wood used for the interior trim and the vanity came from an oak tree that died and fell in our front yard and a walnut tree we needed to take down on a lot we were clearing. The entryway bench was made from a cherry tree we had to remove from a lot several years ago. We used low- and no-VOC adhesives throughout.
Finishes included blueberry bushes in the landscape as well as some native plants that needed thinning from the landscaping of our own home. We did also use some non-native but non-invasive plants in the landscaping like a Japanese Maple to add some specific interest.
All the water fixtures in the house are WaterSense-certified and the toilets are Niagara Stealth with 0.8 gallons per flush and a MaP of 800.
An 80-gallon rain barrel was installed but we did not have room for a rain garden due to the small drainage area and the location of the water supply lines.
At the end of the day, we finished with a Green Built Homes Platinum Net Zero Certification. We appreciate all the work that people put into the home, including the Green Built Alliance for their certification program that encourages more efficient and environmentally thoughtful homes.
Boone Guyton and Claudia Cady have been building houses in the Asheville area since 1993 and have been part of the Green Built Alliance since its beginning as the WNC Green Building Council in 2001.
You can also view this article as it was originally published on pages 22-23 of the 2018-2019 edition of the directory.