There are many ways to link in to the green revolution.
A person can focus on energy consumption, human rights, individual health, environmental protection or a little bit of everything at once, but it is generally driven by a calling in the primitive heart.
This is a tale of how a force of 50 to 100 workers (excluding several hundred offsite producers and innovators) integrated this calling into the Schmeltzers’ home, while factoring in local and global economic constraints.
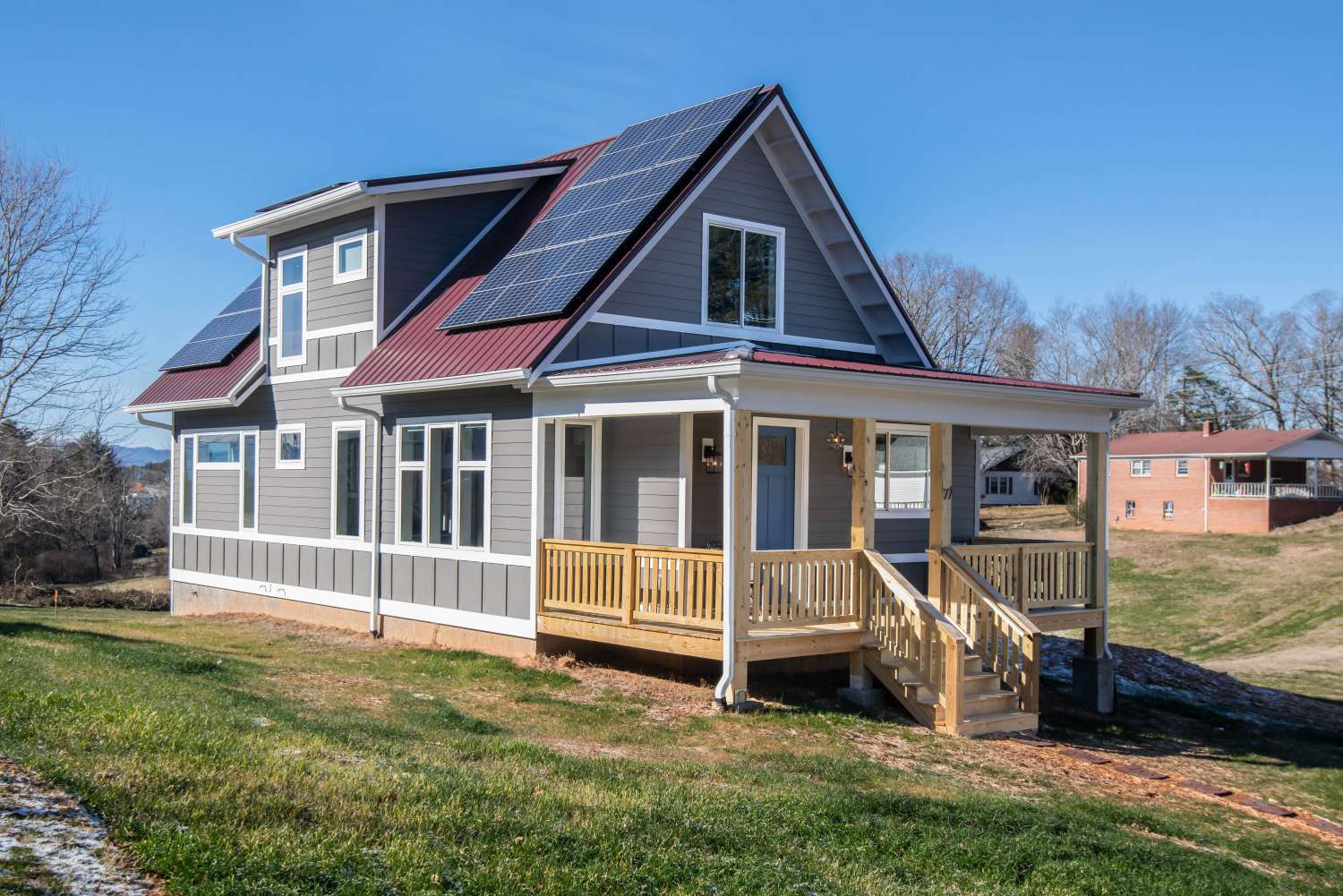
Our journey with Sally and Jason Schmeltzer began in 2017 as they started sifting through local high-performance design-build firms to fulfill their desire for a netzero energy home.
Guided by the Schmeltzers’ commitment to energy efficiency in every decision and product selection, we were able to build a home attaining ENERGY STAR® accreditation and Green Built Homes Platinum Net Zero Energy level certification.
The Schmeltzer home even achieved the lowest Home Energy Rating System (HERS) Score that the Green Built Homes program had seen within any certified project at that time: -10. This was beyond all of our expectations, and the Schmeltzers’ commitment carried the day!
The vision
Sally and Jason moved to Asheville in 2005 to begin their careers as chemistry faculty at the University of North Carolina at Asheville.
As a couple and in their professional work, they always endeavor to make decisions that make a difference (both big and small) for their family, colleagues, students, community, and overall global footprint. This life approach is reflected in their choices to own only one car, join a local Community Supported Agriculture (CSA) program, adopt rescue dogs and prioritize family time.

After living in a 2,400-squarefoot home for more than a decade, the Schmeltzers made the choice to create a home with a much smaller impact on the planet for their daughter and generations to come. After much building-science research, they set their sights on building a new, netzero energy home.
“It was our dream to have a netzero energy home for two reasons,” Sally said. “First, the energy impact; if we could balance the resources our family was using and at least come out even, that would be better for the environment. Second, we saw it as an important financial investment. If we were going to put our funds into a new house, it made sense to us to have one that will be really energy-efficient in 20 or 30 years from now when energy costs go up.”
The couple bought an infill lot with ideal southern exposure in Weaverville, a community that radiates small-town appeal. As the builder, we were passionate about their vision and eager to make their dream a reality. After several design iterations, we arrived at a traditional-contemporary design of a 1.5-story, 1,750-square-foot, 3- bedroom, 2-½-bathroom home.
The Schmeltzers and our project team were deliberate in selecting the most energy-efficient materials and mechanical systems available for the home and budget. The result was an all-electric home, removed from relying on fossil fuels for its operation.
As the project unfolded, we offered the option to upgrade whenever it became apparent that there was a way to achieve greater efficiency at a reasonable cost, and the Schmeltzers frequently accepted the opportunity, which resulted in a higher performance home than we initially set out to achieve.
The design
Incorporated into the structure of the home is insulated oriented strand board (OSB) sheathing with continuous insulation across the home envelope. The windows and doors were strategically designed with both double- and triplepaned glass, and open-cell spray foam fills 2×6 exterior walls to create a well-insulated and air-tight barrier.
These measures were all integrated into a cost-efficient budget with a light and airy interior aesthetic. We also installed a heat pump water heater in the sealed crawl space, which keeps the airspace dry and cool for efficient healthy storage.
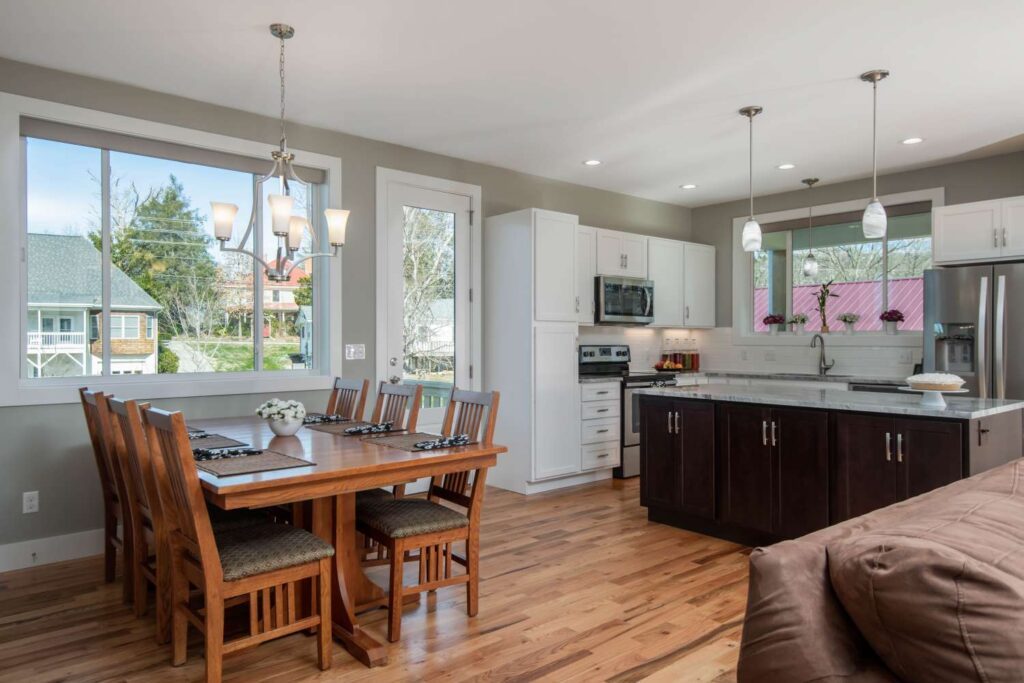
Next steps included selecting an HVAC system. While owners typically think about aesthetic choices when building a new home, mechanical system selection is critical to ensuring the home’s performance, comfort and indoor air quality.
Like many homeowners, the Schmeltzers were accustomed to a ducted system with a natural gas furnace. To explore more efficient, healthier options, we sent them to an open house about variable capacity, split-ductless systems.
Utilizing variable-speed compressors, these systems can be ducted or ductless, are compact, offer zone control and use the precise amount of energy required to meet the comfort needs of the homeowner, thus providing optimized efficiency. Split-ductless systems deliver superior air filtration. Each indoor unit includes a washable, reusable filter, unlike traditional systems that typically have a single filter for an entire residence.
Once the HVAC designer calculated the loads of the home, four wall-mounted split-ductless units were specified, connecting to corresponding outdoor compressors — two upstairs and two downstairs. We also used a jumper duct system, putting inline fans to deliver conditioned air to the closets and bathrooms — ultimately balancing the home’s indoor atmosphere.
After beginning with a net-zero energy qualifying home design with a 21 SEER (Seasonal Energy Efficiency Ratio) mini-split system, our HVAC supplier offered an alternate configuration that boosted the home to above 30 SEER. The Schmeltzers jumped at the opportunity. The units also have a highperformance heating capability, providing comfort in all rooms of their house even during Weaverville’s chilly winters.
As the final step, we focused on indoor air quality.
A common issue with local high-performance homes is negative pressurization, from continuous running bath fans. High-performance homes tout healthier living environments with cleaner, less contaminated air, but negative pressurization can do the opposite, causing harm to occupants or creating bigger issues such as mold, carbon monoxide backdrafting, and moisture concerns. Many builders simply install a continuous running bath fan to qualify their home for green certification. Homeowners frequently disconnect after purchasing the home, which results in unhealthy indoor air quality.
That said, we used an Energy Recovery Ventilator (ERV) for balanced and continuous fresh air for the home, which we install on every residential project.
With efficient materials and mechanical systems plus an airtight thermal envelope, one more step was needed to achieve netzero energy: solar generation. By the end of construction, the Schmeltzers had a photovoltaic system added to their roof and connected to the electric grid.
The net
With their solar generation, the Schmeltzers will actually net positive in warmer months, supplying the grid with energy.
“We officially moved into the house in October 2018 and started monitoring our usage then,” Sally said. “For the month of February 2019, we produced about 600 kWh of energy; for the month of April, we produced 940 kWh.”
In making the jump to build a highly-efficient home, the Schmeltzers have also reaped rebate benefits. Duke Energy provided them with a $3,600 solar rebate, paying a percentage for every kWh generated. They also received a federal tax rebate for building a new-construction home with a photovoltaic system.
This home is a testament to one family’s commitment to high-performance building as a way to secure a better future. Homeowners skeptical about the investment of energy-efficient systems and materials should consider the impact on the planet, the health of their home and the long-term savings in their wallet, as well as the calling of the primitive heart to do better.
Raymond Thompson was carved from the concept that a buffalo robe is the best house ever built. He spent years living on bicycles and in cars across the U.S. and Mexico. He is now on a quest for a future to pass on to his children. Raymond is the owner of Sure Foot Builders. Connect with Raymond at surefootbuilders.com.
You can also view this article as it was originally published on pages 16-17 of the 2019-2020 edition of the directory.