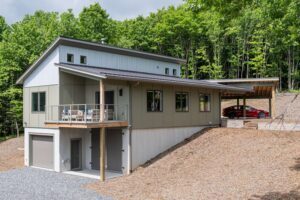
There’s something special about the North Carolina High Country. Home to ski lodges, Christmas tree farms, and quaint downtowns, these remote and rugged mountains offer the perfect place for tranquility and solitude.
Tranquility and solitude were just what Jim and Deb were looking for in their new home. Having spent 13 years traveling in and living out of an Airstream, simplicity had become a way of life for them. They wanted to translate that way of life into a permanent, ecologically friendly home on a high-elevation piece of south-facing land in Ashe County in the northwest corner of North Carolina.
Energy nerds will recognize the area as a cold weather anomaly in our state, with mild summers and a winter more akin to what you might find in Ohio or Pennsylvania rather than in the rest of the south. Building practices designed for cold climates would be necessary to ensure the frugal-energy living that Jim and Deb sought with their home.
A Systems-Built Approach
Jim and Deb selected the “Ridgeline” shell package offered by my company. Based on the net-zero home lived in and designed by Matt Vande of Vandemusser Design, the structural shell components, including open-stud wall panels, roof trusses, and floor trusses, are pre-assembled in our facility in Asheville. We focus on sustainable manufacturing practices, using renewable site electricity to power our operations, and offsetting the carbon associated with shipping our homes to the jobsite through Appalachian Offsets.
The layout is optimized for passive solar heating, featuring a long south-facing main wall and clerestory wall in which to locate thoughtfully sized windows and overhangs designed to shade these windows in summer but leave them open to accept heat gain in winter. With an interior tile floor and stone accent wall offering thermal mass, a high solar heat gain Low-E coating was selected to harvest the maximum amount of heat from these south-facing windows.
The wall system uses 2×6 framing, plywood sheathing plus one inch of exterior insulation and drainable housewrap, offering increased R-value and moisture durability. The roof and floor truss system offers deep trusses for thick insulation levels, and uses a raised-heel truss design. Building the key structural components of a home in a factory allows for very precise construction tolerances, resulting in a structure that fits together very well with few cracks and gaps, further delivering air tightness. Plus, keeping those components indoors until it’s time to go up on site reduces their exposure to the elements, while building in a factory and using parts and pieces sized to match the available sizes of common building materials allows for greater material efficiency. Throughout the build, the project had no need to keep a traditional dumpster on site, and only had to haul waste away from the jobsite four times.
For the foundation, which would be part heated space, part garage (to house the Airstream, of course), Jim and Deb likewise chose a systems-built approach, using a precast and pre-insulated concrete foundation system. The result was a structure that became “dried in” within just a few weeks, allowing the interior finishing to proceed while protected from wind and rain.
An All-Electric Approach
Jim and Deb were very interested in making their home as frugal on energy consumption as possible, and had done the research — complete with spreadsheets — toward that end. I worked with them in my role as a green building consultant for our customers to hone that research. We used energy modeling during the design to consider the energy impact of different options. Minus the wood stove, the home ended up using all-electric appliances, featuring a combination ducted and ductless mini-split heat pump, equipped with hyperheat to offer highly efficient heating, without a backup, even in subzero temperatures. A heat pump water heater located in the basement provides highly efficient water heating, potentially saving $200 a year or more when compared to a regular electric tank water heater. They even used a heat pump dryer.
If you’re noticing a trend with so many uses of the phrase “heat pump,” you’re on to something. By manipulating refrigerants to essentially move heat around, rather than burn a fossil fuel to create it, heat pumps actually output more heating energy than they consume in electricity to run the pumps. Heating, water heating, and clothes drying are some of the biggest energy expenditures in a home, so covering these functions with all-electric heat pumps can have a dramatic effect on home efficiency, and make the home more ready to be powered with renewable solar energy. Jim and Deb hope to add a solar photovoltaic array to their home down the road.
Get the Build Process Right
Jim and Deb also understood the importance of the right building process for ensuring a home is built in a high-performance way.
They used the ENERGY STAR® third-party certification program, which offers a list of above-code practices that must be followed and requires performance testing once the home is complete. This helps ensure that small but critical building science details are not missed.
As part of this process, their home received a final HERS score of 48, indicating a home that is 62 percent more energy efficient than the average new home on the block.
Leigha Dickens is the green building and sustainability manager with Deltec Homes, where she uses a background in physics and environmental studies from University of North Carolina Asheville to educate clients about the science of green building and the interconnected impact of home building. She also manages Deltec’s sustainable manufacturing efforts, and serves on Green Built Alliance’s Board of Directors. Connect with Leigha at deltechomes.com.
You can also view this article as it was originally published on page 34 of the 2021-22 edition of the directory.