Prefab for the Future: New House Factory Aims to Help Affordable Housing and the Environment
By Kristen Alfrey
With home values and interest rates on the rise, there is a desperate need to expand the inventory of affordable housing in our region and around the country.
According to a recent housing report, the median home sale price in Asheville has increased 18 percent during the past year to $425,194. That is simply out of touch with the income levels of many of the people who live in our area.
Creating more affordable and environmentally sustainable building models through intelligent design and conservative land use could very well be the approach needed to create a housing market that is more accessible to the median income household.
Our company shifted to a panelized-wall method of construction in 2021, and is expanding beyond our current panel-building facility to a House Factory on Sweeten Creek Road in Asheville.
The new House Factory will allow us to move toward more complete prefabricated house pieces and full ADUs (Accessory Dwelling Units). We plan to assemble full-length home walls with windows and siding already installed, complete Bathroom “pods” with fixtures, and turnkey prefabricated ADU “building blocks” that could function standalone or be connected for any size home. It’s an exciting time as it takes straight aim at our company mission to be a leader in affordable housing solutions.
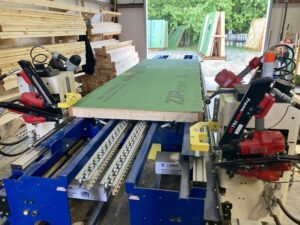
Compared to onsite framing, panel production is a method of building that lowers overhead expenses by reducing material waste and decreasing the time expended in the framing process. In a House Factory, lumber can be cut in advance and pulled to order for a specific panel design. By having a system of standardized panels and using innovative building methods, lumber is cut more efficiently, smaller pieces are used in structural components, and fewer cuts are made because the full length of wood can be completely utilized.
This move has increased efficiency by 20 percent or more. Our team is seeing less than a cubic yard of waste per home, compared with 15 to 20 cubic yards of waste per home with traditional framing. On a typical jobsite, these valuable pieces of lumber would be heading for the landfill. With increased costs of lumber and waste disposal, this can add up to a large sum of squandered resources, reducing the affordability of a home and increasing costs for the builder.
Panelizing also increases the quality of the homes being built, as the cuts are more accurate and the machine squares the walls at the factory, resulting in a higher quality product.
A typical panelized wall can be framed in a House Factory in less than 15 minutes. A pre-built home is stored on crates and delivered to the jobsite where the pieces are lifted into place by a crane or telescoping forklift, and attached by a crew onsite. Each eight-foot section of wall takes about four and a half minutes to lift and set. Because of the reduction of onsite work, less building time is lost due to inclement weather, providing more stable employment for staff and more hospitable working conditions with most of their time spent in a temperature controlled environment. The jobsite is also a much safer place, with lower risk of falls and other injuries.
As far as the impact that panelization has on design and accessibility to quality affordable housing, the possibilities are expansive. With a standardized set of panels, a client should be able to participate in more of the conceptual process by offering the opportunity for them to piece together a home design that best suits their lifestyle and budget, much like putting together a Lego set. This is paving the path towards a business model that could factory build, transport and assemble more affordable, energy efficient, quality-built homes on site — something that the Western North Carolina community desperately needs.
A recent survey of local hospitality workers conducted by the Asheville Independent Restaurant Association offered some interesting insights:
- 89.7 percent of respondents are renters
- 84.8 percent of these respondents said they needed to have roommates to afford rent in the Asheville area
- 85.5 percent of them answered that they spend more than 30 percent of their income on rent or mortgage payments
- 71 percent of the respondents indicated that they would like to purchase a home
This shows that the market for affordable home ownership is strong but we, as builders, may need to adopt more creative solutions to provide the inventory required to close the gap in home ownership accessibility.
With all of the benefits that prefabricated and panelized construction provides — from conserving financial and material resources, improving working conditions, creating more job stability, as well as reducing the amount of waste heading for the landfill — it is proving to be an important tool for the future of building affordably and sustainably.
Kristen Alfrey is a long-time Asheville resident and works for Compact Cottages and Thirsty Monk. She currently spends hours a week sourcing electric panels and appliances, and all the other hard to find things in the home building supply chain. Connect with Kristen at compactcottages.com.
You can also view this article as it was originally published on page 60 of the 2022-23 edition of the directory.